In the previous blog parts, the motivation behind and basic information about the two protocols were given.
Tests at RCs
Recapitulating the main things:
- Autonomous agricultural vehicles (AgVs) are a part of future autonomous vehicles (AVs);
- AgVs have a lot of cable connections that wear down relatively quickly with harsh working conditions and multiple rotating parts of the machines. These cables will be replaced with wireless sensors, therefore, wireless communication protocols have to be investigated;
- Wireless communication on an AgV has to be robust in terms of electromagnetic compatibility because sensors provide very sensitive information about the machine’s conditions that have to be reported timely and correctly;
- An AgV contains a lot of metallic and rotating parts that can create hurdles while sending data;
- Two wireless communication protocols have been chosen to be tested: SmartMesh IP (self-healing decentralised wireless sensor network) and IO-link Wireless or IOLW having the star topology;
- Due to metallic and rotating parts in an AgV, it was decided to start tests on wireless protocols using a reverberation chamber (RC) that is represented by a metallic room with a rotating stirrer. RCs.
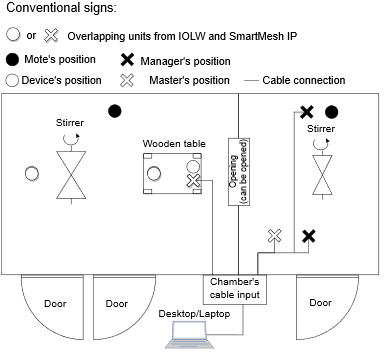
Figure 1 Test setup inside an RC
Figure 1 represents a test setup inside the twin RC located at KU Leuven, Bruges Campus. The twin chamber has a common wall making it more unique in terms of tests that can be performed. In Fig. 1 one may see the positioning of devices that were under test. During the tests, one dependent device (slave) and one main device (master) were used. For some tests, communication was only checked in one RC, for others the opening was used to connect two RCs for more severe communication conditions. The tests can be split into two main groups: line-of-sight (LoS) and non-line-of-sight (NLoS) tests. Therefore test series can be defined as follows:
- LoS test: both the Manager (M) and Device (D) were on the wooden table inside the larger RC (see Fig. 1).
- Non-LoS tests:
- Both the M and D were in the larger RC but while the M was on the wooden table, the D was behind the stirrer.
- The M was in the smaller RC, while the D was on the wooden table in the larger RC.
- The M was put in the smaller RC, while the D was put behind the stirrer in the larger RC.
Table 1. Varied protocols’ parameters
Protocol | IO-Link wireless | SmartMesh IP |
---|---|---|
Parameter | NRTx – number of retransmissions | Publish rate – time delay between to subsequent packets |
TxP – transmission power |
The main test results for the series described above are presented in Fig. 2. Analysing this figure, one may notice that a packet error rate (PER) for SmartMesh IP is slightly better than the one for IOLW for LoS tests. However, it is much higher for NLoS tests. The latency per byte for SmartMesh IP is also higher than the one for IOLW. Already with this information, one could discard the following studies with SmartMesh IP in favour of IOLW. However, one should not forget the specifics of data transmission in the agricultural sector. Sensors should consume as less energy as possible and they transmit data of approximately a few kilobytes a few times per working day. SmartMesh IP has much less current consumption in comparison to IOLW (80 μA and 9 mA per packet, respectively). Taking into account that a payload of one packet of SmartMesh IP is higher than the one for IOLW (80 bytes and 15 bytes, respectively), then one may conclude that the energy consumption of SmartMesh IP is much lower than the one for IOLW. In addition, an AgV is a mere semi-reverberant environment, meaning that it is as not severe as the environment in an RC. Finally, for sensor communication in AgVs latency can be traded off for lower energy consumption. With all these factors it was decided to proceed further with SmartMesh IP and test it on a harvester.
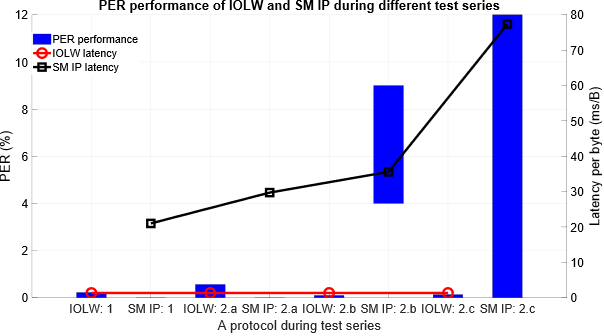
Figure 2 IO-link Wireless and SmartMesh IP results comparison
Tests on a harvester
During the tests in RCs, the main parameter that affected the quality-of-service (QoS) parameters of SmartMesh IP was the publish rate (a time delay between two subsequent packets), therefore the test objective of tests on a harvester was to find out the minimum publish rate for a PER that reaches approximately 0 %.
The actual harvester is shown in Fig. 3, whereas Fig. 4 shows the model of that machine with the sensors’ positioning.
The sensors were put in different positions of the machine to simulate various cases of wireless communication very close to real case scenarios. One of the sensors was also deliberately put underneath the lid to create an obstacle for the transmitting/receiving signal. The position of the Master was also different. It was in the cockpit of the harvester and outside the machine on wooden pallets.

Figure 3 Actual combine harvester

Figure 4 Used model for a combine harvester
During the tests, publish rate was substantially decreased from 6 s (the worst-case scenario inside RCs) to 0.5 s. With this publish rate, most of the sensors had a PER close to 0 %. The furthermost sensor S4 had the maximum PER that was equal to 2.4 and 5 % when the Master was in the cockpit and on wooden pallets, respectively. This means that if a Slave sensor could not establish a proper mesh link with other Slave sensors (S4 had PER>0 when that link was not established, i.e. it communicated directly with the Master), the distance between the Master and that Slave sensor plays an important role.
We may conclude that autonomous vehicles come with big strides in different fields, one of which is the agricultural field. AgVs shall be connected wirelessly not only between each other but also within their internal sensor infrastructure or a wireless sensor network. Two candidates were chosen to be tested for AgVs, namely SmartMesh IP and IOLW. Mainly, due to the lower energy consumption, the former was favoured and tested on a harvester. With a packet delay of 0.5 s, it was possible to achieve almost errorless communication that was considered to be satisfactory for agricultural field purposes. Collaborating with Analog Devices on the work of optimising the SmartMesh IP protocol, it is possible to decrease this packet delay and achieve even better performance.
Future research will also be focused on a uniform technique of recreating the electromagnetic environment of an AgV in an RC to expedite further wireless communication tests in the agricultural field.
This blog contains figures and data that were originally presented in EMC Europe 2022 in the paper: “A Study of Electromagnetic Robustness of IO-Link Wireless and SmartMesh IP for Applications on an Agricultural Vehicle” written by A. Ovechkin, B. Leeman. D. Vanoost, T. Claeys, M. Verhoeven and D. Pissoort. All the authors except for M. Verhoeven are from KU Leuven, Bruges Campus. M. Verhoeven is from CNHi, Zedelgem.
About the Author: Aleksandr Ovechkin
Aleksandr graduated from NRU “MPEI” (Russia) with a Master’s degree which was dedicated to investigating the work of battery chargers during short circuits on the DC distribution systems. Later he joined the structural design engineering team and worked there in the electrical engineering department. While working in a company, Aleksandr didn’t quit research activity and he decided, after getting useful work experience, to completely focus on his research as a PhD student.